Insights
Architect Lives: Building History at Home
By Cassidy O'Hara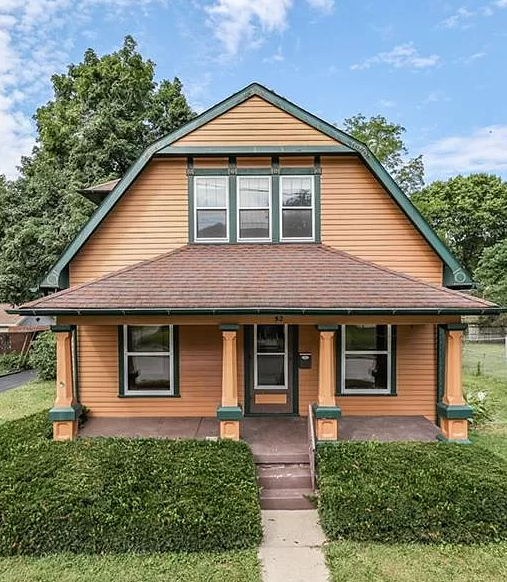
When my fiancé and I purchased our home, I immediately recognized that we were buying a piece of history. Many of the original features remained, including two sets of five-panel French doors, yellow pine flooring throughout, and fully operable double-hung windows with wavy glass and unique brass mechanics. As an architecture student, I was determined to learn more about the history of our house and the manner in which it was built. The construction date and imperfect assembly led me to believe we were in an owner-built kit home.
Kit homes were a popular solution to the working-class housing shortage in the early 1900s. There were many manufacturers of kit homes, the most popular being Montgomery Ward and Sears Roebuck. Sears’ catalog was slightly smaller in size than Montgomery Ward’s, resulting in a clever marketing advantage as it assumed its natural place at the top of the magazine stack.
Sears Ready-Cut catalog homes were first offered in 1914 and included everything required to build a home, excluding masonry and plaster.
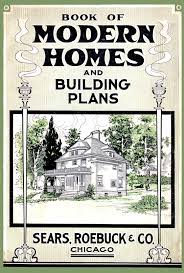
Delivered by rail, each kit included plans, detailed instructions precisely milled and labeled lumber, and all other materials, right down to the nails. The average Sears Modern Home kit had about 25 tons of materials, with over 30,000 pieces and parts. Plumbing, electrical and heating systems were available as add-ons and were not included in the catalog price. It is evident that in our home, these systems were added after construction was completed. There are ducts in odd places, creative plumbing solutions, and more outlets than one could possibly need.
Soon after moving, we met our neighbors, all of whom spoke fondly of “Mrs. Clark’s House”. Mrs. Clark lived in this house for most of her life. According to our neighbors, her father built the house in 1915, a year before she was born. Handy homeowners were encouraged to assemble their own Sears Modern Homes with only the aid of the instruction manual and the helping hands of a neighbor. Mrs. Clark lived here until she moved to an assisted living facility and passed at the age of 104. After she moved, the house was sold to the owners who later sold it to us. As a result, many of the original features were preserved.
Sears is estimated to have sold 75,000 kit homes in the U.S. between 1908 and 1940. Of these, about 90% are still standing. Although many have been remodeled beyond recognition, most are easy to spot if you know what to look for. If you suspect your house might be one of the many Modern Homes that still define America’s vernacular landscape, there are a few guidelines that can help distinguish them from other homes of the same period.
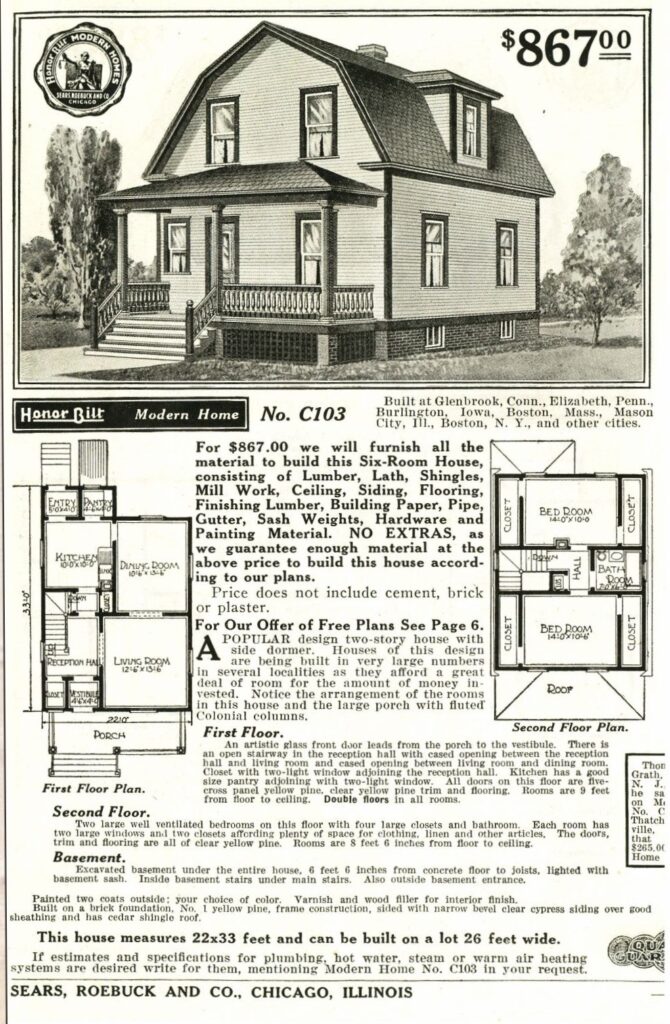
- First and foremost, Sears Modern Homes were only sold between 1908 and 1940. If the construction date falls outside of this range, it is not a Sears home.
- Compare your home to archived catalog images. This is a great resource. I was able to find the catalog ad for our exact model by searching “Sears house, gambrel roof, dormer”. While not an identical match, the Lucerne model is undoubtedly our Modern Home. Customization of the standard plans was encouraged, and up to 30% of Modern Homes were customized and are not an exact match to the catalog ad.
- Consider your location. Kit homes were delivered by rail. The first railroad in our neighborhood opened in 1847, and it was once a central stop on the “Dixie Flyer” and “Hoosier Flyer” interurban rail systems that connected Indianapolis and Louisville.
- If you’re still not sure, look for stamped or marked floor joists in your crawl or basement. Framing lumber in kit homes was stamped with a letter and number which corresponded to the manifest and instruction booklet.
Prefabricated homes are often thought to be the future of design as automation replaces craftsmanship. However, early American prefabricated homes were often the very epitome of craftsmanship; by standardizing architectural designs and optimizing the milling and assembly process, Sears allowed the average working-class man to build a family home by hand. As we return to prefabricated construction methods to solve our current housing shortage, it is more important now than ever, for people and for the planet, to design for the next 100 years.
Creating Ideal Montessori School Environments: A Guide for Architects and Educators
By Carla RemenschneiderMontessori schools are designed to foster independent learning, exploration and creativity in children. As an architecture, interiors and engineering firm, Fanning Howey understands the importance of designing physical spaces that support these principles. By thoughtfully
Full ArticleEsports Facilities for Student Engagement
By Steven HerrAs competitive esports becomes a viable career path, educators across the country are embracing these gaming trends and expanding esports programming at their schools. Schools that have adopted esports are already seeing the benefits. According
Full ArticleCareer Technical Education – Designing a Professional Welding Lab
By Douglas Rich“Career Technical Education (CTE) provides students of all ages with the academic and technical skills, knowledge and training necessary to succeed in future careers and to become lifelong learners. In total, about 12.5 million high school
Full Article